BAKING OVEN

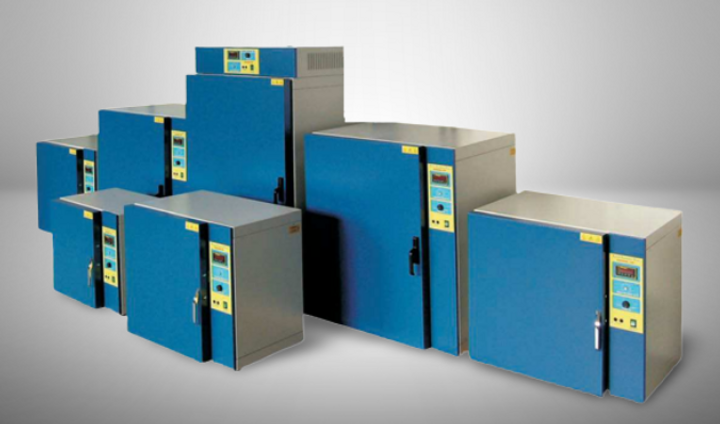
A forced ventilation oven is available in two models: with temperature control only (Sahara) and humidity control (Sahara Dry). They are designed to perform the following works:
​
1. Baking of the PCBs, according to the IPC-1601 standard, should be done at 105-125℃ for 4-6 hours into a forced ventilation oven. All our covers are equipped with a timer, programmable start-up, and countdown mode that is helpful to make sure you do the baking of PCBs only 4-6hours, avoiding the risk of an unnecessary oxidation of the printed board circuits.

2. Baking of SMD components according to J-STD-033 that specify three temperatures: 40℃, 90℃ and 125℃. To ensure <5% RH when baking at 40℃ or 90℃ is recommended the use of the Sahara Dry that are ovens equipped humidity control. How long to bake depends on the moisture sensitive level and package type and body thickness. In the worst case is 79 days for 40℃ baking, 10 days for 90℃ baking and 96 hours for 125℃ baking. Once based MSDs have their Floor Life restored to the initial value. It's important to bake in ovens equipped with a programmable tier command like all the ovens in the Sahara line.
​
3. Thermal cycle. All the Sahara ovens can execute thermal program (easy editable on a PC) useful for testing and for heating/cooling with settable temperature gradient.
SAHARA OVENS
Oven with temperature control only
Compliance with: IPC-1601 Baking PCB
.png)
Temperature Control
Safety thermostat
Ventilation opening
SAHARA DRY OVENS
Oven with temperature control and humidity control (<5% RH)
Compliance with:
J-STD-033 Baking SMD
IPC-1601 Baking PCB
.png)
Temperature Control
Safety thermostat
Humidity Control
TEMPERATURE CONTROL
(Included both on Sahara and Sahara Dry models)

Dehumidification at <5% RH is reached by blowing dry air.
​
The Sahara Dry ovens, unlike Sahara models, are equipped with air-tightness improved internal chamber so as to keep the dry environment achieved without having to continually blow dry air.

The Sahara Dry Ovens must be fed with dry air from 3 to 8 atm.
How much should be dry the air supply?
Normally, centralized systems of compressed air are already equipped with dehumidification system good enough to work properly with this humidity control.
For example, a compressed air system to 7 bar with a dew point of less than 3℃ is usually sufficient.
​
How much is the compressed air consumption?
The dry air is blown into the inner chamber very slowly and only when necessary.
Max consumption: 100 nl per minute
Average consumption: 30 nl per minute
Can be used the nitrogen and what advantages there are?
Yes. The bakin in inert environment reduces oxidation of the PCBs and SMD components.

DATA LOGGER
All ovens are equipped with a data logger for traceability and you can print/save graphs of temperature (for Sahara Ovens) and temperature/humidity (for Sahara DRY ovens)
​
To analyze the logged data and to set the thermal programmer is required the 8107.215 option which include the PidManager software and USB specific cable.
The software is compatible with Windows XP/7/8/10.

Thermal Program:
​
1 Setpoint 40℃ / gradient Max.
2 Wait 20min @ 40℃
3 Setpoint 100℃ / Gradient < 2℃/min
4 Wait 20min @ 100℃
5 Setpoint 150℃ / gradient < 1℃/min
6 Wait 20min @ 150℃
.png)
8107.215

SAHARA 80L Thermal Program

SAHARA DRY 80L 40℃ <5% RH